Optimizing Supplier Audits for Improved Production Standards in the Automotive Industry: A Partner's Perspective
The Importance of Supplier Audits in the Automotive Industry
The automotive industry's relentless drive for precision, safety, and reliability hinges on the quality of every single component. While Original Equipment Manufacturers (OEMs) and their direct suppliers rely heavily on the entire supply base, ensuring consistent quality requires robust processes throughout every level. Supplier audits are a cornerstone of this effort, intended to verify capabilities and compliance. But what happens when audits reveal gaps, or worse, when non-conformances slip through somewhere in the intricate supply chain? How can we truly ensure production standards are met day-in and day-out?
As a dedicated third-party quality control partner (TJ Automotive) supporting OEMs and suppliers across all tiers (Tier 1, Tier 2, Tier N), particularly within the demanding manufacturing sector, we see firsthand the challenges and successes in maintaining production standards. While optimized supplier audits are critical for proactive risk management, effective reactive and ongoing quality control measures are equally vital. Optimizing audits isn't just about improving the audit process itself; it's about strengthening the entire quality ecosystem, including leveraging expert partners for inspection, rework, and containment at any stage of the supply chain.

Why Optimized Audits & Strong Quality Partnerships Matter
n today's complex automotive world – navigating EVs, autonomous technology, global supply chains, and standards like IATF 16949 – the impact of a single non-conforming part, regardless of its origin tier, is magnified. It can trigger:
- Costly recalls and warranty claims
- Production line disruptions affecting multiple levels of the supply chain
- Damage to hard-won brand reputation
- Significant safety risks
Optimized audits aim to catch potential issues upstream. However, when prevention isn't enough, rapid-response quality services become essential to contain problems and keep production flowing smoothly for every player involved.
Beyond the Audit: Addressing Real-World Challenges
Traditional auditing approaches have limitations:
Resource Constraints: Thorough internal audits require significant investment, a challenge for suppliers at all levels.
Inconsistency: Audit outcomes can vary.
Snapshot in Time: An audit reflects a specific moment; continuous conformity requires ongoing vigilance across the tiers.
Finding vs. Fixing: Audits identify issues, but immediate, skilled resources are needed to address non-conformances through sorting, inspection, or rework, whether at an OEM, Tier 1, or any other tier supplier facility.
This is where specialized partners play a key role, bridging the gap between audit findings (or escaped non-conformances) and maintained production standards throughout the value chain.

Strategies for Optimizing Audits (and Leveraging Findings Effectively)
Optimizing audits means making them smarter and integrating their findings into a broader quality strategy that benefits the entire supply network:
- Risk-Based Prioritization: Focus internal audit resources on the highest-risk suppliers or processes. For ongoing monitoring or specific part validations at any tier, consider leveraging flexible third-party inspection services.
- Leveraging Technology: Use data analytics to flag suppliers needing attention. Employ digital platforms for managing audit findings and corrective actions – insights that can also inform where external quality support might be needed within the supply chain.
- Clear Objectives & Scope: Define audit goals clearly. If an audit reveals weaknesses in a supplier's inspection process (regardless of tier), know that expert third-party providers offer specialized gauge and fixture solutions (partnering with certified engineering shops, as TJ Automotive does) and personnel to bolster that capability quickly.
- Enhanced Auditor Competency: Well-trained internal auditors are crucial. Complement their work by having trusted quality liaison support available to manage communications and solutions when issues arise between different tiers or with the end customer.
- Focus on Process Effectiveness (and Swift Correction): Audits should verify processes. When non-conformances are found, fast lead times in containment and rework are critical. Companies like TJ Automotive specialize in providing these rapid, cost-efficient responses to minimize disruption for any affected supplier or customer.
- Collaborative Approach: Foster partnerships across the supply chain. When issues require external intervention, using a neutral, expert third-party can facilitate resolution and maintain positive relationships between tiers.
- Robust Follow-up & Action: Track audit findings rigorously. Use this data not only for supplier development but also to anticipate where third-party inspection or rework might provide a necessary safety net anywhere in the manufacturing process.
The Payoff: Integrated Quality Assurance
Optimizing supplier audits and integrating effective third-party quality control delivers powerful results across the entire automotive supply chain:
Proactive & Reactive Protection: Catch issues early through better audits; contain issues swiftly through expert partners, protecting all downstream operations.
Improved Supplier Accountability: Drive supplier improvement at every level while having measures in place to manage deviations.
Enhanced Product Quality & Safety: Ensure only conforming parts move forward through the supply chain.
Greater Supply Chain Resilience & Flexibility: Respond quickly to quality alerts, minimizing impact on all involved parties.
Cost Efficiency: Utilize specialized external services for inspection and rework where needed, potentially reducing internal overheads and the high cost of disruptions for any company in the chain.
Conclusion: Building a Robust Quality Ecosystem
Optimized supplier audits are a vital proactive tool in the automotive quality landscape. However, they are most effective when part of a comprehensive strategy that includes robust processes for handling non-conformances and maintaining standards continuously throughout all tiers of the supply chain. As a specialized third-party quality control provider serving OEMs and Tier N suppliers alike, TJ Automotive understands the critical need for speed, accuracy, and cost-efficiency when quality issues arise. By partnering effectively – leveraging optimized audits upstream and expert quality services downstream – the entire automotive manufacturing network can build a truly resilient supply chain and consistently meet the demanding production standards required. We are exploring future solutions like automation in warehousing to further enhance these capabilities for our partners across the industry.
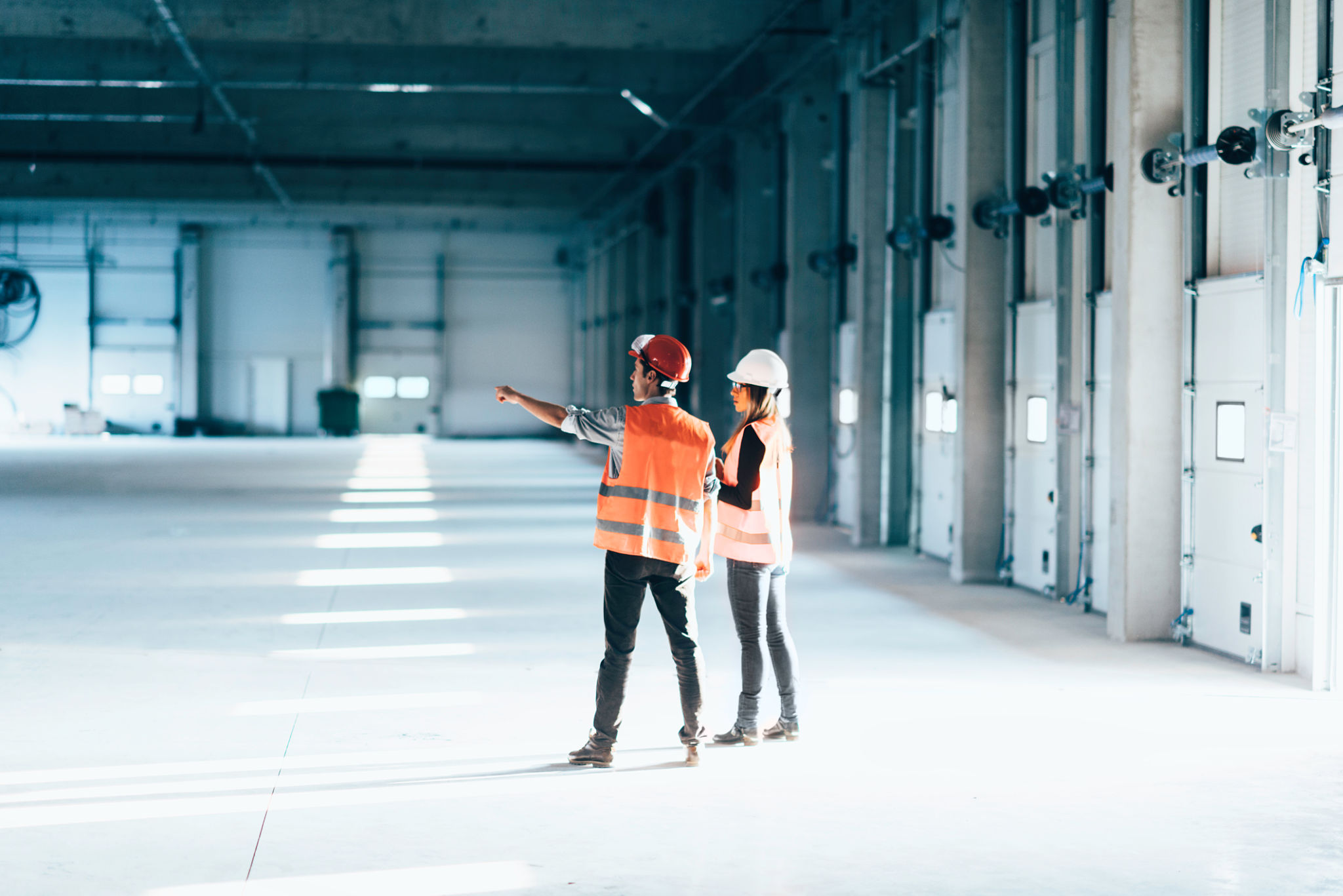
By following these best practices, automotive manufacturers can optimize their supplier audits, leading to improved production standards and a more resilient supply chain. As the industry continues to evolve, staying ahead with efficient auditing processes will be crucial for maintaining competitive advantage.